RoboWeld Precision - Robotic Manufacturing
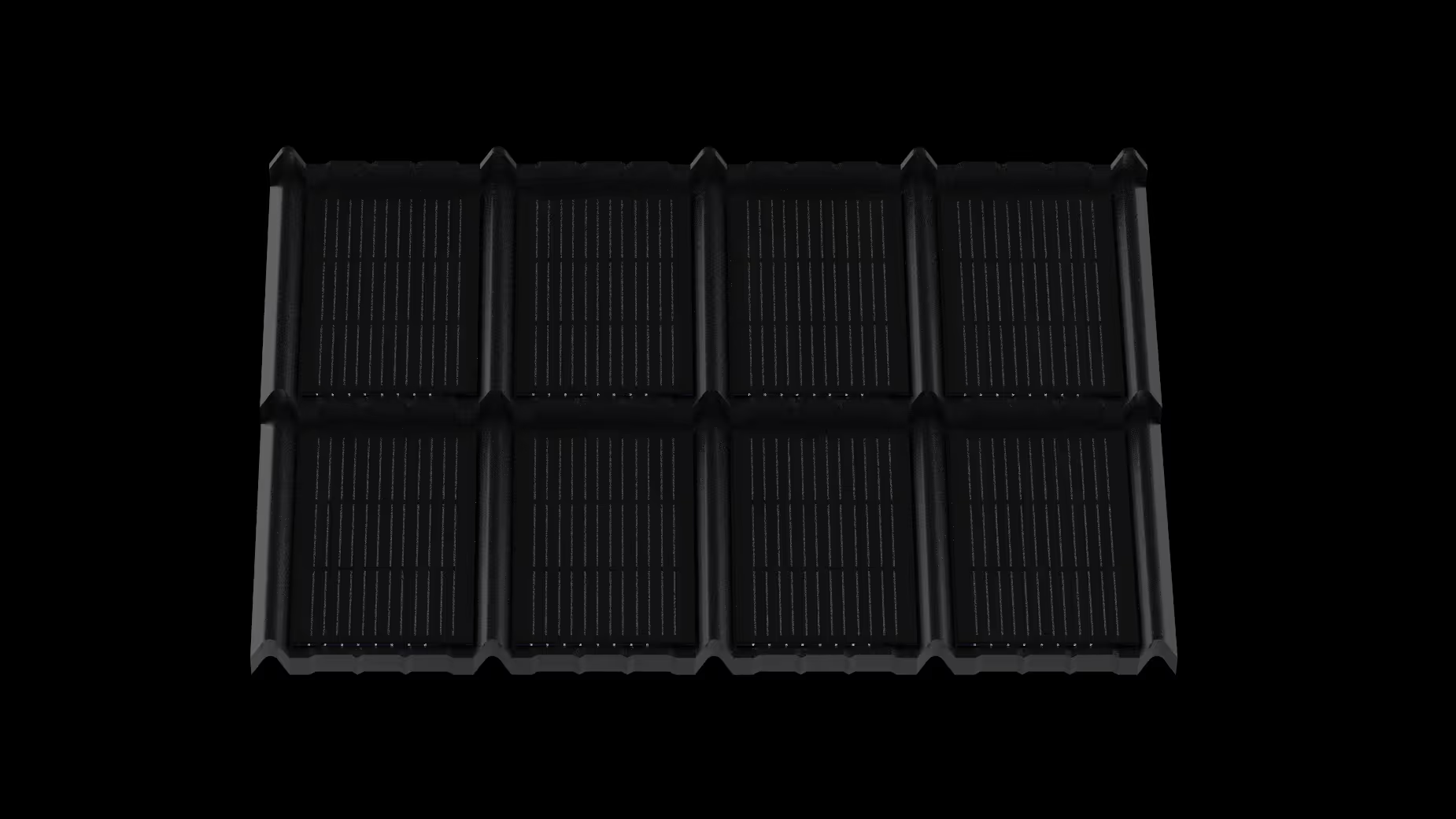
Robotization of solar roof production - how eTile roof tiles are made
From idea to implementation
The problem was complex. In the traditional production of photovoltaic panels, even small millimeter inaccuracies do not matter much - the panel is mounted above the roof on a separate structure. However, in the case of eTile solar roof tiles, where the panel is integrated into the roof sheet, any inaccuracy could have led to a roof leak or a drop in energy efficiency.
We looked for inspiration in the automotive industry, where robots have been providing unparalleled precision in the assembly of car windows for years. It was there that we saw how advanced vision systems and industrial robots can position and connect elements with accuracy to the tenth of a millimeter.
The decision to fully automate production was not easy. It required huge investments in the machine park and a complete change in the approach to the production process. However, we knew that only in this way could we guarantee the highest quality of each solar roof tile produced.
In our factory in Góra Kalwaria near Warsaw, we have created the first automated line in Poland for the production of photovoltaic roof tiles. At the heart of the system are the latest generation of industrial robots, which combine solar glass, photovoltaic cells and roofing sheet with extraordinary precision. Each stage of the process is monitored by vision systems and sensors that verify the accuracy of the execution with a precision of up to 0.1 millimeter.
Today, after years of perfecting the process, we can proudly say that we have created a production system that guarantees the repeatable quality of each tile produced. It is this precision of workmanship that makes our solar roofs not only beautiful, but above all reliable and durable.
In the next part of the article, we will take a closer look at how exactly our robotic manufacturing process works and what technologies we use to ensure the highest quality of each element of the eTile system.
Robotization of solar roof production - how eTile roof tiles are made
How Robotic Manufacturing Works
The eTile solar roof tile production process is a fascinating journey through the world of advanced automation. In our factory near Warsaw, industrial robots work with a precision that the human hand cannot achieve, creating a product that combines the functions of roofing and energy source.
It all starts with a detailed quality control of the input components. Advanced vision systems inspect every sheet of sheet metal, solar glass and every photovoltaic cell. This is a crucial stage - even the smallest imperfection could affect the tightness of the roof or the energy efficiency.
The heart of the process is the precise joining of the solar glass to the roof sheet. Robots apply a special binder with an accuracy of 0.1 millimeter, using the same technology that has proven itself in the manufacture of automotive glass. The temperature and humidity control system in the production hall provides ideal conditions for the binding of materials.
The next step is the integration of photovoltaic cells. This is the most demanding moment of the process, where robots must maintain absolute precision. Each cell is positioned using laser measurement systems, and special sensors control the pressure force - too large could damage the fragile link, too small would not ensure the correct connection.
Particular attention is paid to electrical connections. Robotic arms perform microwelding of wires with precision inaccessible to humans. Each connection is then tested for conductivity and mechanical strength.
The quality control system works at every stage of production. Industrial cameras and sensors collect data on each manufactured module, forming detailed technical documentation. If any parameter deviates from the norm, the system automatically stops production and marks a defective element.
At the end of the production line, each solar tile undergoes comprehensive testing. We check not only the electrical parameters, but also the tightness, mechanical strength and aesthetics of the workmanship. Only after the positive passage of all tests is the product allowed for packaging and shipping.
In the next section, we will look at how this precision and quality control translate into real benefits for eTile solar roof users.
The Future of Solar Architecture
In the world of architecture, a fundamental change is taking place, similar to the one we observed with the window revolution. Until 20 years ago, single-glazed windows were the standard - today no one can imagine a house without double or three-glass packages. The same thing happens with photovoltaics - it ceases to be an addition to the building, and becomes an integral part of it.
Imagine the architecture of the future. In 2029, EU regulations will come into force requiring the installation of photovoltaics on all new residential buildings. But this is not the distant future that we can fear - it is an opportunity we can seize today. InvisibleSolar Finish allows you to stay ahead of these requirements by creating buildings that not only meet future standards, but set new architectural standards.
This technology opens up particularly interesting opportunities in conservation areas. Take, for example, historic city centers - places where any change in architecture is carefully analyzed by a monument conservator. Traditionally, the installation of photovoltaic panels would be unthinkable here. However, with the ability to perfectly match color and texture to historic roofing, InvisibleSolar Finish creates a bridge between the past and the future of architecture.
We are also seeing how this technology is affecting the real estate market. A house with invisible photovoltaics is not only lower electricity bills - it is an investment that retains its value over the years. Just as no one today wants to buy a house with outdated windows or without thermal insulation, in the near future the lack of integrated photovoltaics will be seen as a serious real estate shortcoming.
Our vision of the future is an architecture in which energy production is as natural as thermal insulation or ventilation. We are working on the next generations of InvisibleSolar Finish technology, experimenting with new glass tinting methods that will allow us to better combine performance with aesthetics. In parallel, we are developing intelligent energy management systems so that every kilowatt of energy produced is optimally used.
What seems like an innovation today will become the standard tomorrow. InvisibleSolar Finish is not just a response to upcoming regulations—it's a vision of architecture where technology serves aesthetics and buildings discreetly produce energy while retaining their architectural identity. This is the future we can build today, roof by roof, building by building.
Subscribe to the newsletter
Get a handful of information about solar technologies from Electrotile